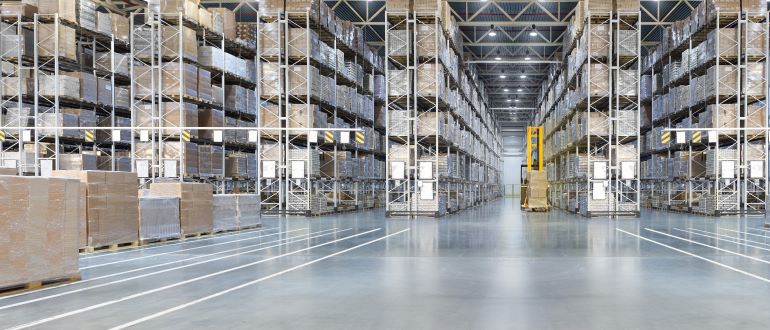
While the age of the manual warehouse is coming to a close, it’s no slam dunk that simply implementing smart warehouse capabilities and technologies will automatically lead to an optimized and more efficient warehouse. In fact, implementing smart warehouse technologies incorrectly can actually decrease the productivity of the warehouse.
“I’ve seen sites that have gone full automation without planning,” says Keith Moore, CEO at warehouse orchestration provider AutoScheduler.AI. And by full automation, Moore means these warehouses have all but eliminated workers. “They essentially have people who unload the trucks, and from there, everything is automated. The only human interaction from that point is watching the automation. It’s impressive. But after they invested tons of money into their automation, they’re now only running at 60 percent of the throughput that they were running before the automation.”
But when done correctly, the benefits of smart warehouse technologies are substantial. “The advantages include greater productivity, enhanced accuracy, improved inventory control, and increased customer satisfaction. Yet, the cost of implementation, the requirement for substantial changes to procedures and workflows, and the possibility of disruptions during the transition phase can all be difficult,” observes Jayesh Jain, senior vice president at Sage Software Solutions.
How do organizations automate their warehouses wisely for improved results? Below are the five keys to success:
Baseline your warehouse data. “Data is useful in knowing where your gaps reside and predicting events and conditions, such as things that can impact availability. You can quickly identify what was a mistake, what worked, give feedback to managers, and understand what will increase employee efficiency,” says Kevin Beasley, CIO at ERP provider VAI.
“There’s a logical flow in how you acquire your data, and you need to figure out how to best make that data uniformly available,” adds Moore. “Data visibility is the first stage, attained by consolidating your data from various systems. There are a lot of tools out there to help people do that,” he says.
Consider building your “operational twin.” Once the warehouse data has been baselined and conditioned for use by data visualizers or warehouse management systems, the next step is to model how the warehouse can be run optimally. “I don’t use the phrase “digital twin,” any longer because the term has been warped beyond usefulness,” Moore says. Moore contends with a digital twin; organizations are trying to model their warehouse operations down to every physical nut and bolt. “But there’s no digital twin for an entire warehouse that can accurately model forward the next 24 to 48 hours. That digital twin just doesn’t exist.”
“The more appropriate term is an operational twin,” he adds. The operational twin consists of having all your warehousing data available in one place, which can be analyzed by machine learning/AI and optimized for warehouse operations.
“While every warehouse has different processes, workflows, and people, they all have the same objective. Things come in and go out, and the longer things are there, the worse off you are. A warehouse is designed to be a flow-through in the supply chain. It’s all about flow in and flow out. And everything in between companies building out processes to make sure that model adapts to their business, and that can be modeled in an operational twin,” Moore says.
With that operational flow in place, organizations can become more predictive about what will happen when conditions change. “This gives you a more prescriptive view into what is most likely to happen and where your constraints may be so that you can potentially shift the sequence of operations to maximize for an outcome,” he says.
Choose the right technologies for the warehouse. Whether AI, IoT, robotics and automation, location devices, or other new shiny technology — it’s crucial that the technology fits. Beasley notes that many warehouse managers deploy new technologies that don’t necessarily fit within the environment. “One example is that people are trying to use inexpensive mobile phones as barcode scanners. They don’t realize that they come with many limitations, such as they can’t be used to scan from 40 feet up in the air,” explains Beasley.
Consider outside support. Moore points out that many warehouse managers aren’t data scientists and don’t tend to have data scientists on staff, so he advises warehouse owners and operators to strongly consider contracting such talent. Beasley agrees. “Whether or not you’re going to have a consultant come and advise you depends on your abilities,” says Beasley.
Outside support can also come in the form of training. “Setting up a smart warehouse system may call for major adjustments to workflows and processes. Enterprises should invest in training and change management programs to assist staff in understanding and adjusting to the new system to achieve successful adoption,” says Jain.
Start with one set of technologies and expand from there. According to Beasley, it’s ideal to start with one technology, maximize the returns on that investment, and expand upon technologies from there. “Perhaps the technology doesn’t give you the returns you expended. Now, you have the resources to focus on that and adjust. You won’t if you set out to try to automate everything at once,” he says. While it may sound straightforward, this is where the data baselining and operational twin can play a significant role in understanding the current state of the warehouse and the best optimization paths forward. “Understanding the current status of the warehouse, including its procedures and technological infrastructure, is crucial to implementing a smart warehouse system. This can assist in locating areas that can be automated and optimized,” says Jain.
While implementing smart warehouse technologies may be challenging — and implementing new technologies always is — doing so intelligently is the only way to surpass (or even keep up) the competition. ”
“What was considered smart a number of years ago isn’t considered smart today,” says Beasley. “Things like barcode readers and RFID are standard,” he says. The same will be true of the leading technologies today. The differences will become how well these technologies are implemented and orchestrated.