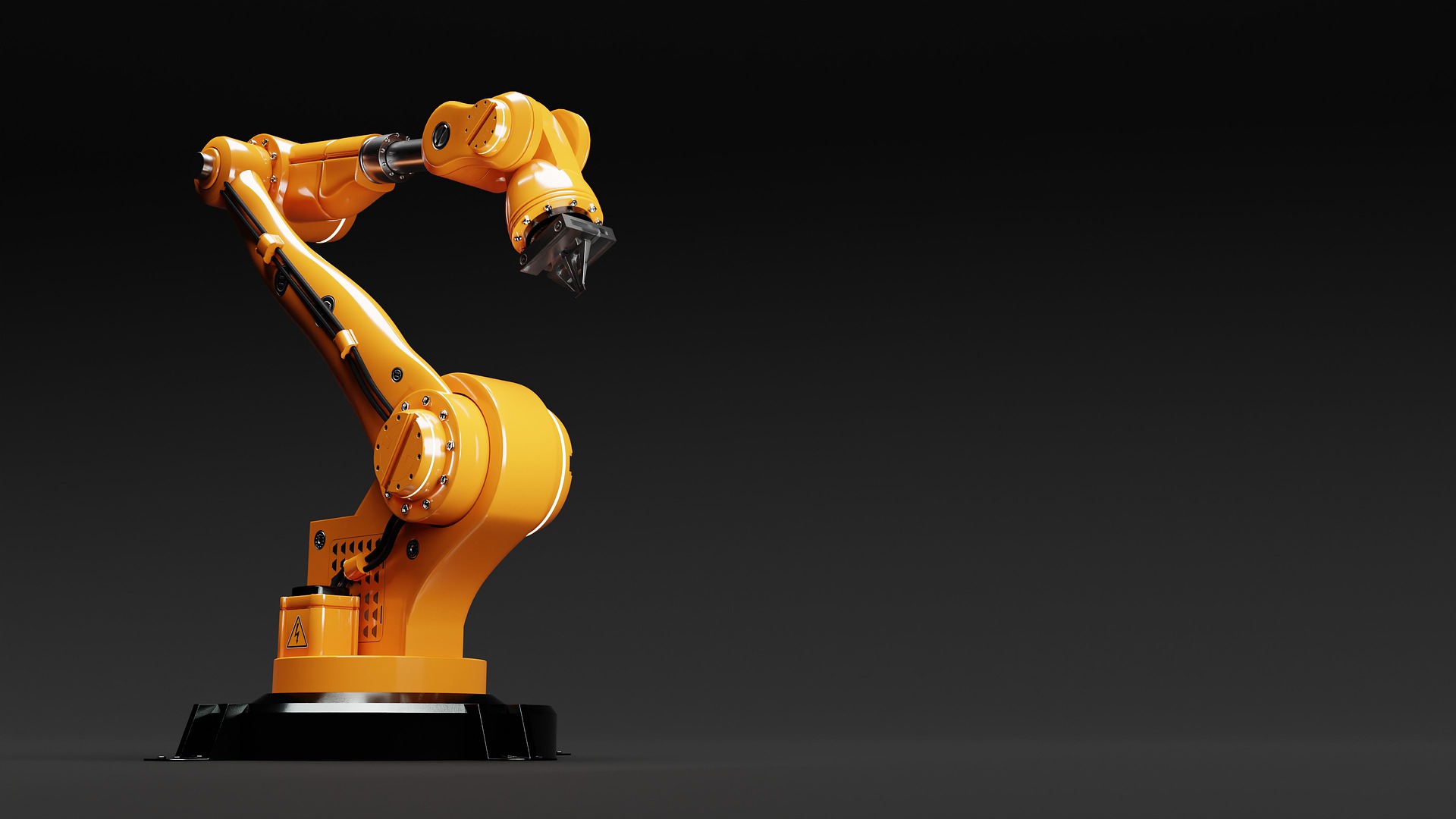
Mitsubishi Electric just dropped two new robotic arms, and they’re built with both design and functionality in mind, according to the Tokyo-based company.
The robot arms aren’t your typical factory bots. They don’t have batteries, which takes the worry out of replacing them – an activity that causes down time, and in hard-to-reach areas may require special tools or temporary displacement, or readjustment of the arm altogether.
The MELFA RH-10CRH arm is capable of lifting 10 kilograms, and is designed to handle high-speed transportation and assembly, which makes it a natural fit for food and automotive production lines. The RH-20CRH model has more muscle, can lift up to 20 kilograms, and is suited to lifting and packaging heavier objects.
The arms offer advanced functionality, tracking operations, support for 3D and 2D vision sensors and force sensing to ensure precise performance for high-speed tasks.
“These improvements to productivity are amplified by a simplified design that significantly reduces the number of components, resulting in up to 69% weight reduction compared to previous models. This lowers installation and facility costs while enhancing long-term operational reliability, continuous operation performance, and overall productivity. Furthermore, the integrated wiring and air piping within the robot arm reduce wiring complexity and simplify setup.”
“With the RH-CRH series, we’ve created a solution that delivers exceptional performance and addresses the practical challenges our customers face in modern manufacturing,” said Keisuke Matsumura, Development Section Team Leader. “These robots alone demonstrate our commitment to innovation by helping manufacturers enhance productivity and efficiency. Additionally, when combined with other Mitsubishi Electric’s software advances – such as MELSOFT VIXIO enabled AI visual inspection, the creation of digital twins using MELSOFT Gemini – the expansion of automation, additional cost savings and system benefits can be achieved.”
The arms can be a solution to worker shortages, according to the company, “providing manufacturers with greater flexibility in adopting digital manufacturing while addressing skilled workforce shortages. These new robots enhance industrial automation through high-speed operation, easy installation, and exceptional efficiency. Compact and lightweight, they are ideal for manufacturers aiming to boost productivity while navigating space and weight constraints.”
Robotic arms have come a long way since the first industrial robotic arm, “Unimate,” was made in 1959. George Davol, the creator, was given a patent for it in 1961.
According to Universal Robots, a company that specializes in its own version of robotic arms, the original purpose of the devices was to provide a precision force multiplier, first in the automotive industry. “The first robot was installed at a General Motors plant in New Jersey to assist a hot die-casting machine. The company Unimation (an abbreviation of Universal Automation) was created and it went on to develop robots to assist with welding and other applications in the fast-growing automotive industry. By 1966, Unimation granted licenses to Nokia in Finland and Kawasaki Heavy Industries of Japan to manufacture and market the Unimate, expanding the use of programmable robot arms into a global market.”
The automotive industry remains, by far, the largest market for robotic automation, followed by the electronics assembly, food and beverage, and metal and plastics manufacturing, according to Universal Robots, which has sold more than 100,000 Cobot arms.
Universal Robots has six versions of the Cobot, and recently released its heavy lifter, the UR30, capable of lifting 30 kilograms. It has a 51.2 inch reach. “With the ability to handle higher torque, the UR30 opens the door for precise screw driving and the 30 kg payload brings productivity to everything from machine tending with multiple grippers to palletizing heavy parts.”
Perhaps the most specialized application of a robotic arm is in the field of medicine, or surgery to be more exact. The da Vinci Surgical System uses four thin robotic arms to assist surgeons in delicate, or minimally invasive, procedures, from cardiac surgery to incontinence procedures.