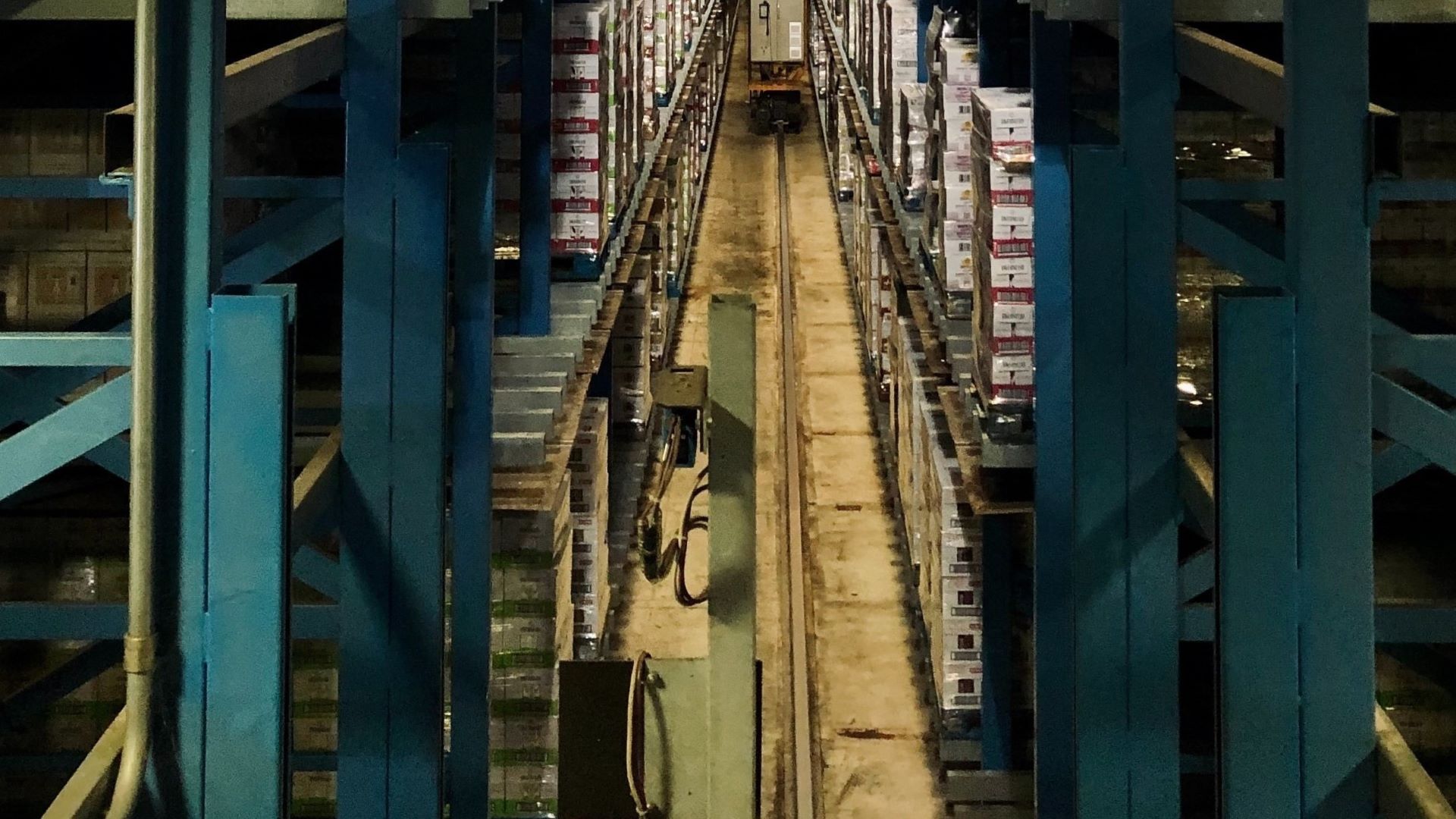
While manufacturers have historically been known to be resistant to change, change in the manufacturing sector is underway in a big way. Specifically, nearly every manufacturer recently surveyed expressed that they’re either already underway in their move to smart manufacturing, or they will be within the year.
Still, headwinds to success remain, but those who successfully make the transition hope they’ll find enhanced operational resilience, increased productivity, cost-effectiveness and better real-time decision-making — all of which could bring a competitive advantage.
To gauge manufacturers’ current relationship with smart manufacturing-associated technologies, industrial automation and digital transformation provider, Rockwell Automation, conducted a survey among consumer package goods manufacturers (CPGs). Respondents cited a number of obstacles to their successfully adopting smart manufacturing technologies — obstacles that exist within their own organization, and those that exist externally.
Roadblocks to Smart Manufacturing Abound
First, what is smart manufacturing? Smart manufacturing is the term associated with using technology to build manufacturing efficiencies and operations. The technologies covered under smart manufacturing include internet-connected machinery (Industrial Internet of Things), data analytics, and the continuous monitoring of production processes. Smart manufacturing also utilizes AI/ML, and virtual and augmented reality. Some see smart manufacturing as the fourth stage of the industrial revolution.
The most significant internal challenge survey responses cited this year (as well as the 2022) are consumer package goods, manufacturers’ ability to successfully balance profitable growth and overall quality. Furthermore, 36% of respondents believe that the deployment of technology and the use of data represent significant internal challenges. And particularly, 35% of consumer package goods manufacturers surveyed cited worker retention as a key internal issue, with 34% concerned about improving employee onboarding.
Other considerable challenges cited include deploying and integrating new technology and understanding data to improve the business. However, the most significant obstacles to growth remain external barriers largely out of the manufacturer’s control. For instance, 52% of consumer package goods manufacturers cited inflation as their biggest current challenge, while supply chain disruption was cited by 41%, and the shortage of skilled workers at 38%.
The Race for Business Digital Transformation in Manufacturing
These challenges, however, are proving to also be a catalyst for change. According to the Rockwell Automation survey, when asked what consumer package goods manufacturers were doing to improve their business outcomes, the top response was to improve their use of data analytics (44%), 44% to improve quality; and 43% cited a fear of missing out as they are accelerating their digital transformation efforts in an attempt to keep up with the moves of their competitors.
To better track their data, 63% of respondents turn to software, while 57% use process automation to automate their business processes.
The dearth of warehouse employees properly skilled for the manufacturing digital era is one of the reasons why respondents may be avoiding layoffs or staff reductions. A full 90% of consumer package goods manufacturers report keeping their workforce the same or adding more workers to their payrolls. Also, 48% of respondents report that they’re turning to process automation to address their shortages in labor.
Additionally, 38% expect to repurpose their existing workforce and 29% believe they’ll actually hire more workers due to technology adoption. As we covered in Manufacturing Workers Eager to Upskill, those working in this sector are eager to keep pace with technological change.
Smart Manufacturing Comes of Age
In Amanda Razani’s recent interview with Jerry Foster, CTO at Plex, he shared his thoughts about why some manufacturers may lag. “They’re not quite sure how to take a holistic view of their process, of their operations, and put something in place that they are confident will cover that whole end-to-end [smart manufacturing process] in their facility,” he says. “They look at what’s available to them, and they’re not sure if that’s going to work or if this is going to work. And you know, manufacturers often go with the “If it’s not broke, don’t fix it” mentality.”
Sometimes, Foster explained, manufacturers need a “little nudging” by revealing to them the return on investment that’s possible with the untapped potential for improvement in many facilities. “One of the things that we’re always trying to do is increase efficiencies and have better quality and measure everything that was happening from one end of the facility to the other, including the customers and suppliers on each side,” Foster says.
That nudging may no longer be necessary. Seventy-eight percent of respondents believe smart manufacturing is very important to the future success of their business. Despite that knowledge, only 49% of respondents report that they’ve already adopted smart manufacturing. Still, most of those remaining, or 45% in total, claim that they’ll be adopting smart manufacturing within the year.
In total, respondents have either adopted or plan to adopt smart manufacturing initiatives for quality management systems (55%), production monitoring (55%) and enterprise resource planning (55%).
Keeping pace with market transformations (31%), mitigating the pandemic’s impact (31%) and addressing cybersecurity (28%) ranked as the top ways smart manufacturing has helped consumer package goods manufacturers overcome obstacles and mitigate risk.
Smart manufacturing initiatives for enterprise resource planning most frequently report having the biggest ROI in this sector, with supply chain planning and quality management systems also showing promise.
While these initiatives demonstrate tangible ROI and prove value, there are still meaningful barriers to adoption across the CPG industry.
The primary barrier? Cost. Forty-four percent of respondents said that either a lack of knowledge (41%) or skills (39%) are the two top barriers to the adoption of smart manufacturing initiative adoption. Two of the other barriers that smart manufacturers can control and improve internally are: A lack of knowledge (41%) and a lack of skills (39%).
In his interview, Foster noted a technology that he believes will make a significant impact on manufacturing — AI. “Smart manufacturing and digital transformation is all about connecting people, machines and software, and then collecting data from all of those connected processes and using that data to your advantage.”
The 2023 State of Smart Manufacturing report surveyed 216 CPG C-suite executives in 13 countries and gathered responses regarding their current state of technology in manufacturing, the biggest challenges and the future of the industry.