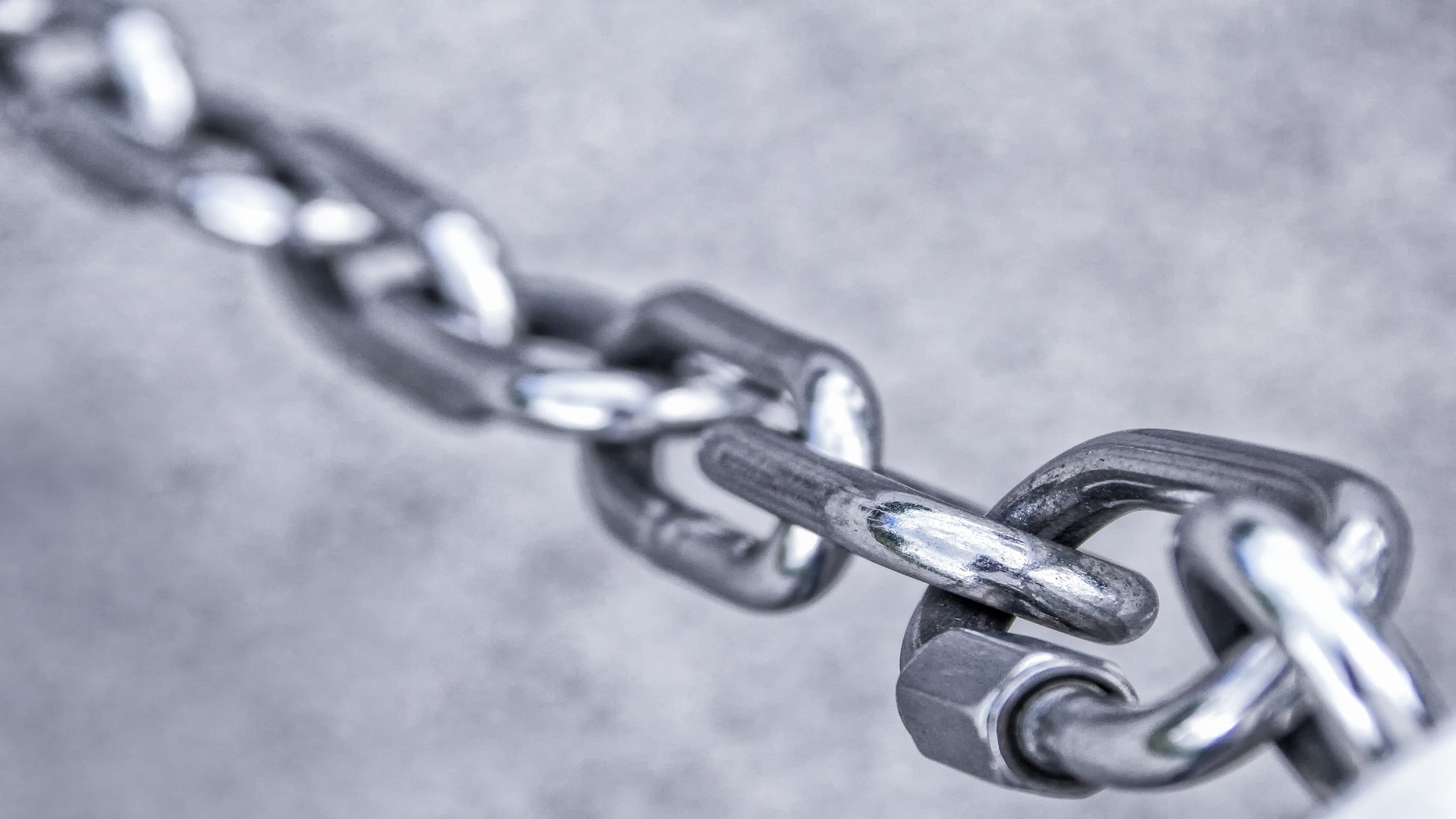
Digital transformation drives manufacturing success. According to recent survey data, 80% of manufacturing companies surveyed implement new technologies for supply chain optimization, business intelligence and production line planning.
Technology isn’t enough, however, to help businesses streamline operations. Making the most of new solutions requires companies to successfully bring staff on board — a task often made more difficult by significant resistance to change.
Let’s break down the top change concerns and offer four strategies to help manufacturing companies reduce resistance to successful implementation.
The Top Change Concerns
Changes don’t happen in a vacuum. When companies bring in new systems, software or other digital solutions, both people and processes are impacted. It’s possible to predict the impact on processes, however, people are more challenging.
For employees, three concerns about change are common:
- Limited familiarity
Many manufacturing -companies rely on legacy solutions that are years or decades old. From custom-built production line systems to in-house legacy software, these tools are often integral parts of operational processes.
As a result, staff are intimately familiar with legacy technologies. They understand both the benefits and drawbacks of legacy solutions and are experts at getting the most from these tools in the smallest amount of time.
New solutions mean new processes to learn. While these processes may be significantly more efficient than current operations, they’re also unfamiliar. This limited familiarity often leads staff to prefer legacy tools even if new solutions are demonstrably better.
- Increased complexity
Staff are also concerned about increased complexity. Unlike older solutions, many new tools are delivered using as-a-service models. This means they often rely on connected, cloud-based frameworks to deliver improved performance and accessibility.
For staff, new solutions come with the worry of more complexity. Employees are concerned that technology may add more work and responsibilities to their role without streamlining current processes.
- Reduced job security
The advent of artificial intelligence (AI) and process automation in manufacturing may lead staff to worry about their job security. For example, if AI tools offer improved quality control or production line management, employees are worried that new technology will lead to layoffs. As a result, they may be reluctant to adopt new solutions or adapt workflows to include them.
Four Strategies for Reducing Resistance
Change naturally comes with resistance. With the right approach, however, manufacturers can reduce the impact of change on people and processes.
Four strategies can help streamline success.
Bring in employees ASAP.
The sooner staff are part of the change process, the better. By communicating with staff about why technology changes are necessary, what’s going to change, and when change will likely happen, employees feel like part of the conversation.
This provides a measure of control over the change. Instead of simply being given a new tool and a few training classes before they’re told to implement changes at scale, staff have time to process the idea, research the solution, and get more comfortable.
Demonstrate key features.
It’s also worth demonstrating key features of new technologies before they go live. For example, if companies are deploying a new enterprise resource planning (ERP) system, it’s a good idea to bring staff in for an informal training session so they can see the product in action.
By showing teams how the new tool works — including how it’s similar and how it differs from current solutions — companies can reduce the risk of employee pushback when new solutions are deployed.
Take action on feedback.
No product is perfect. While new solutions may represent a significant upgrade from current tools, there’s always room for improvement.
To increase change acceptance, ask staff what they think. Let them explore new systems and workflows and give their honest feedback on what works, what doesn’t, and what needs to be improved. Wherever possible, take action on this feedback.
For example, if staff notes that login processes are cumbersome, manufacturers can take action to implement single sign-on (SSO) solutions that help streamline user access.
Provide a clear roadmap.
Finally, it’s important to give staff a general timeline for implementation. While this timeline is subject to change based on deployment challenges and operational constraints, planning helps staff more effectively make the transition.
This could mean backing up key files or digitizing critical documents. It could take the form of training classes to become more familiar with new solutions, or it could be meeting with colleagues to develop effective team strategies for adoption.
Making it Work
Success for manufacturing companies means consistency. Consistent performance, consistent output and consistent quality. Digital transformation helps make this possible. From software solutions to hardware automation to the advent of artificial intelligence, technology delivers on the potential of Industry 4.0.
Making the move, however, isn’t always easy. Staff are often uncertain about the impact of change and worried that it will negatively impact their job security, autonomy or ability to complete tasks on time.
Making it work means having a plan. While businesses can build a comprehensive plan on their own, it’s often beneficial to partner with manufacturing and supply chain planning providers. Equipped with both industry knowledge and technology expertise, these providers can help companies more effectively manage resistance and more successfully implement new technologies.