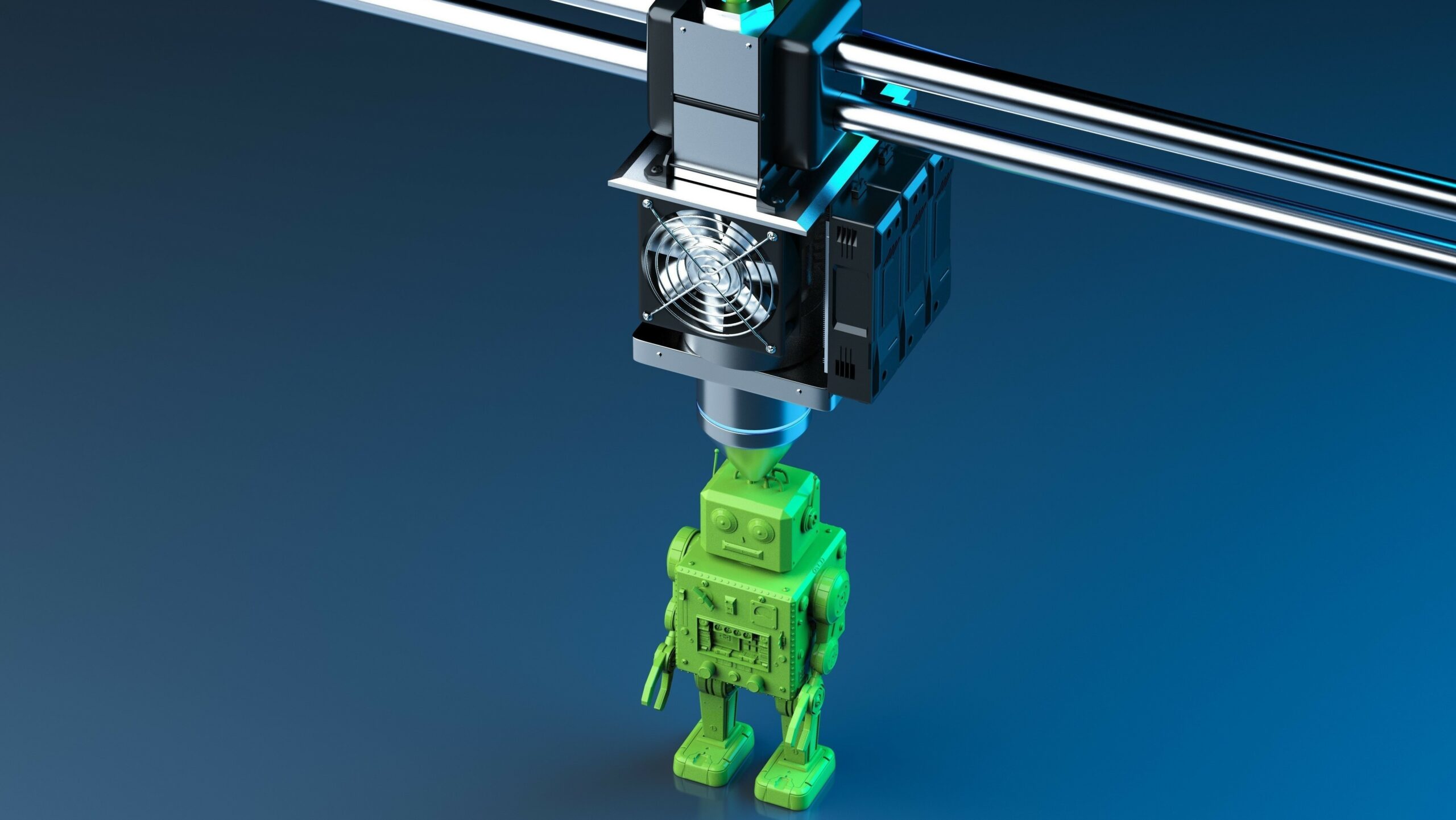
The manufacturing industry is poised for a radical digital transformation with the advent of Robots-as-a-Service (RaaS) and 3D technology emerging as flexible, scalable and adaptable solutions to production.
The emergence of RaaS promises a more dynamic manufacturers ecosystem where robotic solutions can be tailored to precise needs, for as long as they need them.
In addition, RaaS lowers the entry barrier for customers that can now get the benefits of robotic manufacturing without having to purchase expensive equipment, hiring expert personnel and dealing with material suppliers.
This shift in manufacturing practices has the potential to reshape factory floors, streamline processes, and revolutionize the way products are conceived, designed and brought to market–with the end resulting being the rise of so-called “lights out”, or fully automated, production facilities.
One company focused on this technology is the Swiss startup SAEKI, which recently emerged from stealth mode with $2.3 million funding round. The company wants to build fully automated plants with industrial robots using 3D technology.
As part of the RaaS model, customers get a certain level of customization, either of the robotic cell, or the materials or software, to custom tailor the manufacturing machine to their exact requirements.
“Often when buying a 3D printer, it’s sold as a do-it-all magic machine; the reality is when working at a large scale, all links in the chain matter and optimizing them can improve the quality of our parts, lower cost and improve lead time for our customers,” explains Matthias Leschok, co-founder at SAEKI.
He notes RaaS makes especially good sense for industries which are not digitized yet– for instance, the construction sector.
“Here we have identified a big fear of change or adapting to new technologies,” Leschok says. “RaaS provides our customers with the opportunity to get direct access to the newest technologies without the capital and operational expenses.”
SAEKI directly enables the fabrication of bespoke elements without the need for their customers to go through a long learning period.
“However, these fundamental benefits can be also brought to other sectors, where robots can help to overcome labor scarcity, safety concerns, or increase efficiency,” he adds.
In the aerospace and automotive industry, composite materials (mainly carbon fiber composites) are used to build lightweight, but strong structures.
To manufacture composite component tools, molds and jigs/fixtures are required to shape the carbon fiber cloth into its final shape, to aid during the curing process, to trim excess material, and to hold the structure during bonding processes.
All these steps require custom tooling that is traditionally made from carbon fiber itself and/or machined out of a block of solid foam, then coated multiple times to get a hard surface.
“Making a tool is not only time intensive, but the materials involved are quite costly, especially when most of it is machined away and scrapped,” Leschok says.
When looking at an aircraft, composite parts can become quite large (from 0.5 to 15/20m) and conventional tooling manufacturing starts becoming even more material inefficient and overall expensive.
“What we are proposing is a drastically different process: We 3D print a near net shape mold, tool, or jig by using carbon fiber reinforced plastics; the same robot machines, only the necessary surfaces, minimizing material waste, then inspect the tool with an optical measurement device to verify that the part is within tolerance,” he says.
Pedro Pacheco, analyst with Gartner, explains the transition to RaaS has already begun, however a series of challenges stand between the concept of a “lights off” manufacturing facility and today’s reality.
“If SAEKI or some other company shows up with a great robot that can do a lot of stuff in manufacturing, and even if the technology really works, that by itself is not enough,” he says. “You will have to convince manufacturers that this really works and adopt business models that can fully leverage the technology. As we as we have seen many times in the past, it’s not easy. You need to have a disrupter.”
Pacheco notes the investment and implementation has just as much to do with the change management willingness of an organization as it does with the capabilities the technology itself offers.
“The need is there, no doubt,” he says. “Let’s imagine there is a robot that could automate the assembly of an entire large ship – that would be fantastic, because in the end, cost will go down, production time will go down, and quality probably will go up.”
The opportunity for leaders in the manufacturing industry to digitally transform operations and introduce more automation is near, but how quickly they will adopt this technology is the question.