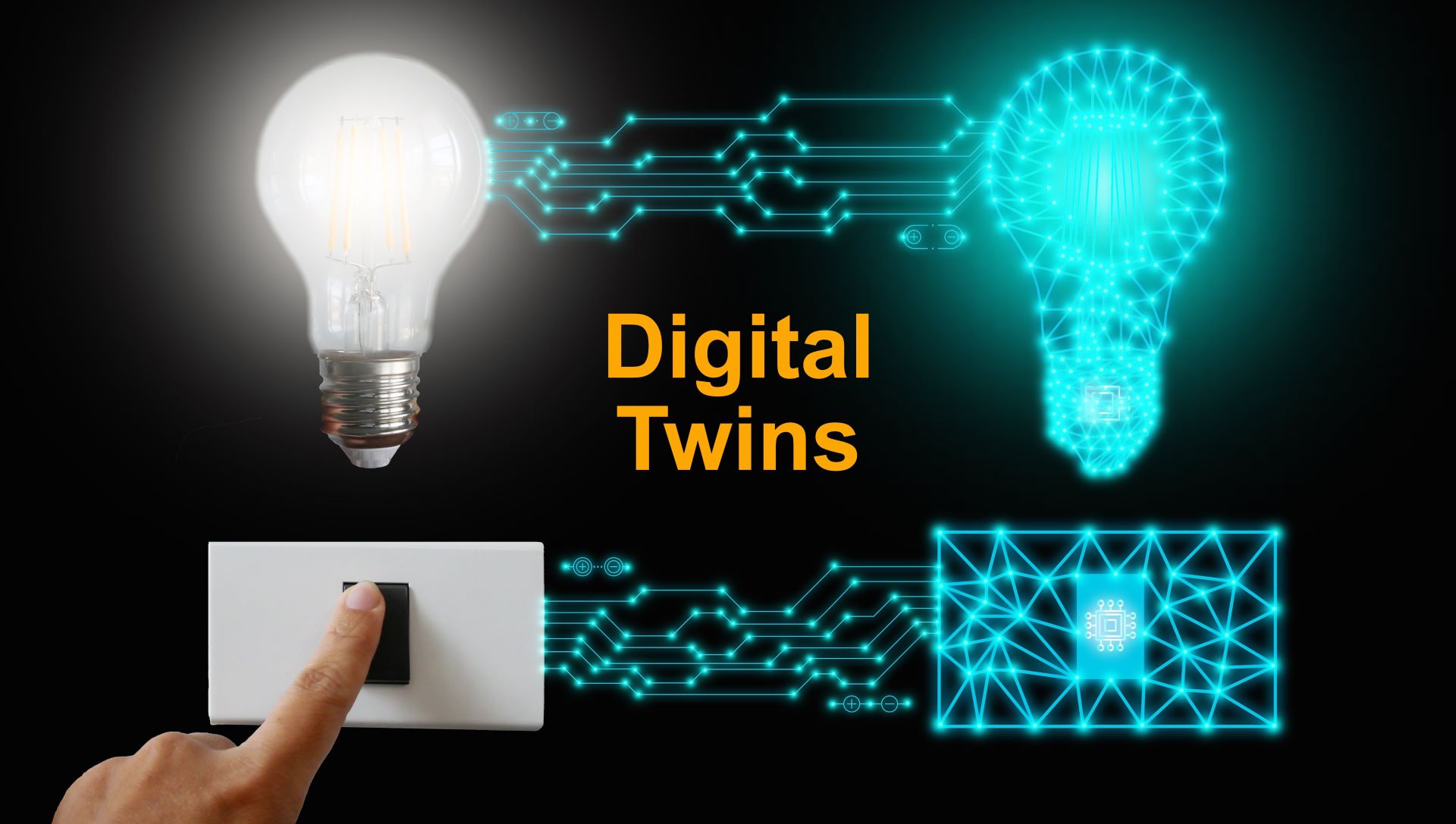
While the “digital twin” concept has existed for over 20 years, digital twins have yet to catch on within manufacturing fully. These synchronized virtual representations of physical-world entities or processes have been primarily limited to the production of large-scale, complex, and expensive products, such as within the automotive and aerospace industries for new automobile and aircraft development, or large energy projects such as wind farms power plants, and oil and gas facilities. That’s changing for several reasons.
First, technologies such as cloud computing, machine learning, edge computing, and ubiquitous networks, among others, are now in place, making digital twin implementation more accessible to enterprises. Second, the move to Industry 4.0, smart factories, and the need to improve process automation and product development efforts drive increased demand for digital twin technologies.
However, according to KBV Research, digital twins do have headwinds such as privacy and security concerns, lack of interoperable standards, lack of skilled staff, and significant upfront investments required. However, the benefits can be substantial for organizations that implement digital twins. That’s expected to drive substantial growth in digital twins. The overall digital twin market, also according to KBV Research, is expected to grow from about $13 billion in 2022 to $195 billion by 2023.
In an interview last year, ScaleOut Software CEO William Bain explained to DigitalCxO’s Mike Vizard that digital twins have been, to date, essentially a technology for large-scale scale, expensive and complex product design. “People have thought about this term digital twins as at a high level of encompassing all aspects of the design in software that matches a physical entity, usually a single large, complex entity,” Bain said. The broadening of digital twin demand beyond such use cases is driving demand.
Ilya Smirnov, head of AI/ML at Usetech, says he’s overseen successful implementations of digital twins in modern chemical plants, transportation and rail companies, and oil and gas refineries. “We’ve developed, using digital twins, safety systems for railroads,” he says. Smirnov and other experts say effective digital twin implementations provide:
Superior Predictive Maintenance. Unplanned downtime is expensive. It’s costly in manufacturing. Digital twins enable the creation of virtual replication and simulation of physical assets so analysts can simulate performance using virtual models and increasingly perform real-time analysis of equipment performance so that system and device failures can be more accurately predicted, avoiding unplanned downtime.
Augmented product development. Through the creation of virtual models of products, manufacturers can more cost-effectively test and validate product design ideas and potentially even optimize performance before beginning production. This can also help shorten the time to market.
Improve operations. Entire manufacturing processes can be modeled with digital twins. This helps manufacturers analyze all manufacturing processes and model potential strategies to optimize resources and improve effectiveness.
Improved Collaboration. Through a distributed virtual model, teams representing various aspects of the manufacturer can collaborate, such as engineering and design teams, data science teams, production and operations teams, quality control and maintenance teams.
Improved analytics. Data from many sources — sensors, floor machinery, manufacturing line data, design data, inspection data, environmental data and user and historical data — there’s no shortage of data to improve the digital twin. Because of all this data, digital twins can improve analysis and decision-making in operations, quality control and manufacturing optimization.
Streamline costs. Because digital twins provide unparalleled virtual simulation capabilities, manufacturers can optimize production processes, take advantage of cost savings associated with predictive maintenance, perform rapid virtual prototyping and optimize inventories.
Overall, digital twins provide manufacturers with a powerful tool for gaining operational insights, optimizing processes, improving product quality and driving innovation, ultimately leading to increased efficiency, productivity and competitiveness.
“I’ve seen amazing digital twins,” recalls Tony Fernandes, CEO at UEGroup. “When designed right, they can appear to be very real. At an aerospace company, someone once left the digital twin of an aircraft running, and it appeared as if the aircraft was running out of fuel, and it appeared to be real. It sent alarms and emailed people in the building, and quite a few of us thought we were watching a plane out of fuel. Digital twins that allow for that kind of abstraction work well,” Fernandes says.
In upcoming stories, we will examine how to build, deploy, manage and secure digital twins successfully.