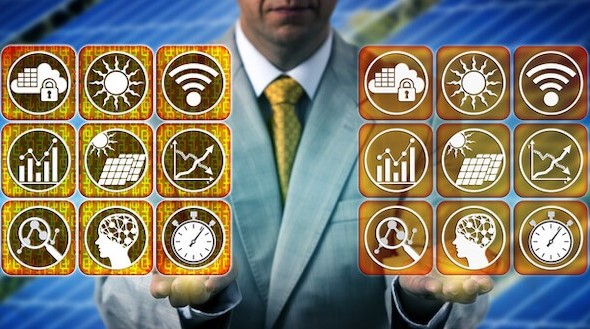
Value stream management is on the rise. According to the last report from the Value Stream Management Consortium, about 21% of respondents are implementing or already using value stream management techniques. One of the simplest methods to get started is value stream mapping. However, it has some challenges. One is that it is just a picture capturing a state in time of a dynamic system, such as a process. Another is that, even though you can spot a problem, it still doesn’t give you an idea about the impact on the value stream if you have implemented a solution. The last one is that there are no backward flows on the map; even though everyone knows about their existence. Examples include: Defects/bugs, merge conflict, deployment/update failures, etc.
Defining Value Stream Management
Value Stream Management is a management technique or practice that focuses on increasing the flow of business value from request to customer delivery.
Value stream mapping (VSM) is a lean tool that employs a flowchart visual representation approach to documenting every step in the process.
Digital Twin Technology
The manufacturing industry has completely changed the socio-economics of our lives. Now, at full speed, we are witnessing the next iteration of industrialization; by adopting digital technology, we are collectively gaining effectiveness and more efficiency. Industry 4.0 is a revamped approach to production and manufacturing that goes far ahead of static value stream mapping and uses the Internet of Things and cyber-physical systems to collect and analyze large amounts of data. Manufacturing facilities are highly automated and digitized, using self-optimization, self-configuration, and artificial intelligence to improve cost efficiencies and produce higher-quality goods or services.
The manufacturing field gave birth to the digital twin concept that combines physical and virtual spaces for a product.
A digital twin is a digital representation of an intended or actual real-world physical product, system or process (a physical twin) that serves as the effectively indistinguishable digital counterpart of it for practical purposes, such as simulation, integration, testing, monitoring and maintenance.
A digital twin disrupts the entire product lifecycle management (PLM), from design and manufacturing to service and operations. With a digital twin, companies can have a digital footprint of all of their products throughout the entire product lifecycle, from design through development to consumption. Digital twins make the manufacturing process highly efficient since they collect data from thousands of sensors, feed data into a fully functional replica of the entire factory and leverage AI and machine learning, making better operational decisions and achieving the next frontier of productivity. A digital twin makes complex systems simple to observe, understand and explore their behavior within the digital world.
We believe that software or digital product development processes should not fall behind such a powerful technology that has transformed the landscape of the manufacturing industry. We see that today value stream management solutions are primarily focused on showing the current picture of the flow, providing the value of the business intelligent solutions. However, it is dismissing the opportunity to gain more productivity through data interpretation and multidimensional optimization, enabling a continuous improvement cycle even further. We envision a blending of the value stream management systems with the powerful simulation and AI technologies that can unfold answers to future-looking questions like what would be the value stream performance if we changed the team topology. What would be the ROI from rework reduction or shift-left implementation? How much should we grow the team if we need to double the throughput?
Let’s take a look at what the digital twin of the value stream can bring to a company.
First of all, you can start with a simple simulation. As an experienced technology leader, you create a value stream map in some shape or form, often implemented as a static picture. Given the classical notion of value stream mapping, it is rather easy to convert it into a process-like simulation mode. Here is an example of such a model. Value stream simulation enables you to not only see the holistic picture and establish a common language among teams, as you can do so with a value stream map, but also experiment and explore how your value stream behaves under different circumstances with different flow structures, or the impacts of different organizational structures. Moreover, you can explore, for instance, what would happen if you implemented a shift-left strategy for quality assurance so that engineers would work hand-in-hand with quality engineers to deliver a value increment. Or, given what the simulation model highlights in the value stream bottleneck, you can explore various options to tackle, such as:
- To what extent do you need to increase capacity, and what would that role be? What would be the next bottleneck once you removed the identified constraint?
- To what extent should you remove waste (reduce rework, for instance) affecting bottleneck activity?
- Can you run several activities in parallel?
You can run each of the scenarios under different loads: The features demanded to be produced, different effort distribution involved in a feature implementation, various engineering productivity scenarios, and so on.
The true power of the digital twin in value streams is realized when the simulation model is connected to the underlying systems and actually transformed into a digital twin. Of course, this allows companies to enable continuous, close-to-real-time performance monitoring. However, on top of that, due to the simulation model, such monitoring can predict future operational challenges. So value stream architects and agile enterprise leaders can provide objective and quantitative arguments explaining how a specific decision may affect the overall performance of the digital product delivery. The conversation about operational performance and how to improve it can help swing a conversation from political bombshells and finder-pointing to objective and evidence-driven debates. If we take a fresh example of layoffs happening in the tech field that often include unfair blind cuts of a certain percentage of the workforce, then we can see that there is no consideration of how such a decision might affect operational efficiency in both long and short-term (such as culturally through diminished psychological safety); or if there is an adverse effect, how the operating model could be changed, what we trade off in time-to-market, utilization, cost, etc. The ability to explore the implications of a possible decision and the opportunity to evaluate for the optimal one can bring a competitive advantage over regular players that cannot see two steps ahead.
As you might assume, a manual search for an optimal decision might be tedious and not productive, and this is where artificial intelligence solutions add value, enabling people to look for optimization among multiple dimensions, given their unique constraints and environment.
If you are interested in learning more about value stream simulation and the digital twin of the value stream, you can sign up for a free-of-charge webinar, where we cover practical methods of value stream mapping, demonstrate the transition from mapping to simulation modeling, shed light on how to evaluate optimization scenarios and advise on the proper roadmap to build a full value stream digital twin to empower continuous improvement with the power of predictive capabilities.