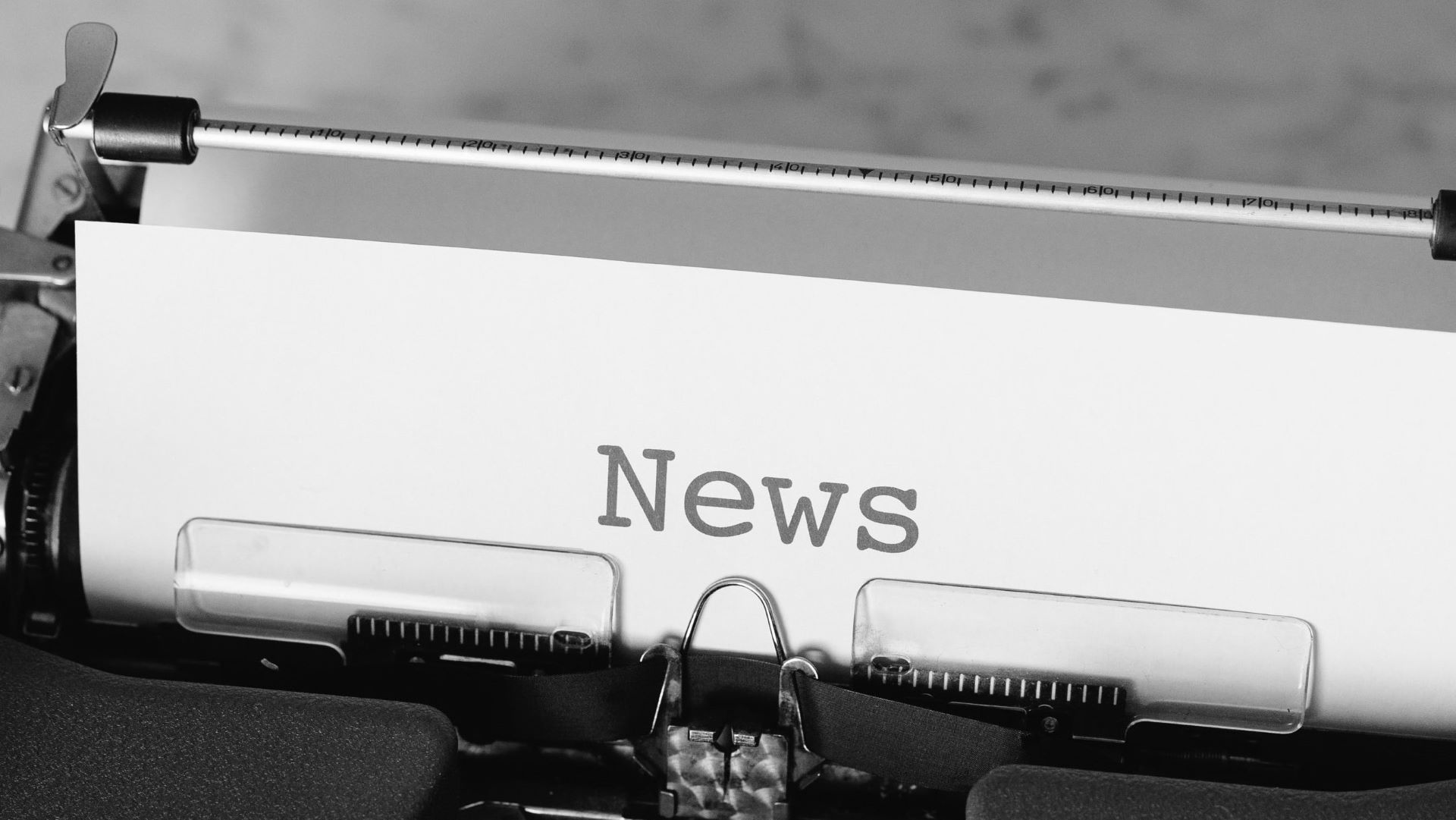
Wearable technology specialist Ultrahuman, designer of a smart ring designed to track health metrics, announced plans to open a manufacturing facility called the “UltraFactory” in Indiana.
The opening of the factory will help the company accelerate its production capacity and expand its market presence in Ultrahuman’s fastest growing market.
The Ring Air, which utilizes advanced sensors to monitor parameters such as heart rate, activity levels, sleep quality and stress levels, is part of Ultrahuman’s broader ecosystem of health-focused wearable technology.
Among the company’s other products is a continuous glucose monitoring wearable called the M1 Live, a home health device called Ultrahuman Home, and a preventive blood testing product called Blood Vision.
Mohit Kumar, founder and CEO of Ultrahuman, said the opening of the UltraFactory, based on the company’s first operational model in India, will add a production capacity of 200,000 smart rings and would open within the next six months.
“Typically, biosensor manufacturing facilities don’t require a lot of space—you don’t do a lot of hydraulic work or machining work,” he explained. “Our production facility looks more like a lab and less like a factory.”
While he declined to give the specific location within the state, he noted due to the compact footprint required to make the Ring Air, an urban location would be completely manageable.
“It’s physically constructed, it just needs to be made production operational,” he said. “We could do almost $100 million worth of production in 15,000 square feet area which is an extremely high ROI.”
Kumar said the establishment of a manufacturing facility in the U.S. would help the company lower costs in shipping and logistics, while aiding the US government in its push to strengthen domestic manufacturing rather than manufacturing in offshore locations, like China.
He also pointed to an expected hiring boom of 150 new Ultrahuman employees in the US over the next 12 months, split between engineering and research (30%) and commercial operations (70%).
“We want people to help us scale up production, and we also want to move research staff from across the U.S. to our production facilities,” he said. “A lot of the talent innovation we were looking for in this space is actually in the U.S. market, on the embedded devices side, on the sensor research side and on the algorithms side.”
He said he believes Ultrahuman would benefit by having a research and development presence in the U.S., working closely alongside the manufacturing component.
“This is exactly how our original UltraFactory in India also operated, with all the research and production happening together,” Kumar explained. “We want to replicate the model in the U.S.”
He said when it comes to actual production of wearable devices, there’s a lot of research that helps determine how one goes from making a few thousand devices a day to 100,000 devices a day.
“That science is also intertwined with what type of sensors we are creating, because making 100 sensors is not the same as making 1,000 sensors, and that’s different from making 10,000 sensors,” Kumar said.
He explains in biosensor manufacturing, a combination of manual and automated processes is used, with lightweight components handled by robotic arms.
Integration and assembly involve automated soldering and quality checks, incorporating machine learning and computer vision to identify and reject defects.
Ensuring accurate testing of bio signals presents challenges, as replicating various scenarios requires extensive human testing.
To address this, machine learning and digital signal processing are employed to mimic human body signals, allowing for comprehensive testing against expected outputs.
“Overall, both integration and testing processes are fully automated and driven by computer vision and machine learning techniques,” Kumar said.
He added because these devices are designed to be space-efficient and require more automation than traditional manufacturing methods, they’re suitable for production in the U.S.
“This allows for the creation of new devices, all of which will be locally manufactured to ensure independence from international supply chain disruptions and talent issues, while also nurturing local talent,” Kumar said.