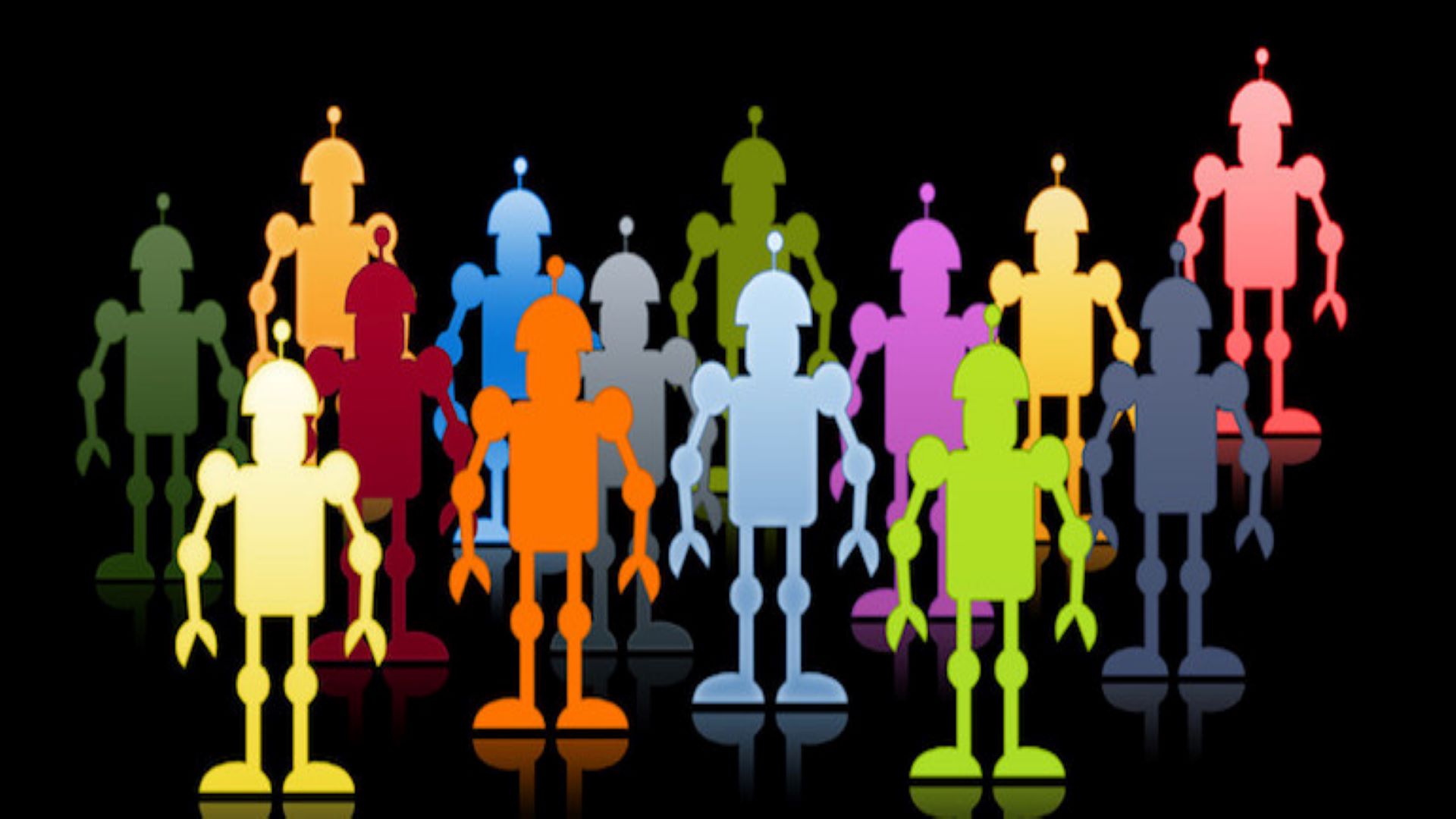
The Toyota Research Institute (TRI) recently showed off new capabilities for its Punyo robotic platform, engineered to tackle everyday tasks demanding more than just manual dexterity.
The Punyo project focuses its efforts on empowering robots to perform complex tasks involving the manipulation of large and unwieldy items using their arms and chest.
The “soft” home robot leverages its design characteristics to amplify human efforts in handling bulky objects and facilitating precise manipulation, as a TRI YouTube video of Punyo holding bags of groceries demonstrated.
The approach complements TRI’s existing efforts in fine motor control and grip-based dexterity, providing a holistic solution for a wide range of practical scenarios.
Traditionally, robots for manipulation, for example factory robots, or the arms of most humanoids that have been displayed lately, are intended to make contact only with their hands/grippers, and this is generally inefficient.
Alex Alspach, senior manager of dexterous manipulation at TRI, explains the team is on a mission to help with everyday tasks that require more than just hands and fingertips.
“The surfaces of their arms are generally built with slick metal or plastic surfaces,” he says. “For some of these robots, if they do accidentally make contact with their arms with an object, they cannot sense the item, and this can lead to dangerous situations.”
Covered with compliant materials and equipped with tactile sensors, Punyo’s hands, arms and chest can feel and adapt to contact, ensuring stability, increased friction and evenly distributed forces during manipulation.
Compliant materials in the context of robotics refer to materials that possess certain flexibility or elasticity, allowing them to deform or absorb energy when subjected to external forces.
These materials are used in various components of robots to enhance safety, adaptability and interaction with the environment or humans.
Underpinning Punyo’s soft exterior are two “hard” robot arms, a rigid torso frame, and a waist actuator, combining the precision and reliability of traditional robotics with the compliance and sensing capabilities of soft materials.
The arms are covered with air-filled bladders, or “bubbles,” which can be individually pressurized to adjust stiffness and enhance compliance.
Features like Punyo’s “paws”, high-friction latex bubbles equipped with cameras for sensing, further enhance its manipulation capabilities. These paws, along with Punyo’s arms and torso, enable it to perform a wide range of tasks.
“It is a lightweight, low-cost solution to challenges faced by other designs,” Alspach says. “Its compliance, friction, and willingness to make a lot of contact result in stable grasps with evenly distributed forces, and its tactile sensing allows these forces to be controlled and informative.”
He adds the systems TRI is designing can augment any traditional robot and turn it into a soft, contact sensing robot arm.
To facilitate learning and skill acquisition, TRI has developed advanced teleoperation tools that allow users to teach Punyo whole-body manipulation skills.
These tools, such as the Grasp Synergy Teleop and Hierarchical Operational-Space Teleop, enable intuitive control over Punyo’s movements and facilitate the development of complex manipulation strategies.
Alspach says looking ahead, TRI aims to further refine Punyo’s capabilities through reinforcement learning and plan-guided techniques.
“Our research is centered on exploring and addressing the diversity of situations our robot will experience in simulation and in the real world,” he says. “This is critical for our robot learning pipeline.”
By combining simulation-based planning with real-world demonstrations, TRI seeks to enhance Punyo’s autonomy and enable it to learn new skills independently.
He explains Punyo is “eagerly” making a lot of contact and fully sensing every bit of a surfaces or surfaces.
“This data collection is incredibly useful and critical as TRI’s teams dive deeply into learning methods for generalized, capable robots,” he says.
He points out the team – who are experts in soft robotics, contact-rich planning and learning, tactile sensing, and human-robot interaction – are dedicated to a future where robots and people collaborate safely, productively and happily side by side.
“Our latest achievements with Punyo are an important step in making this a reality,” he says.