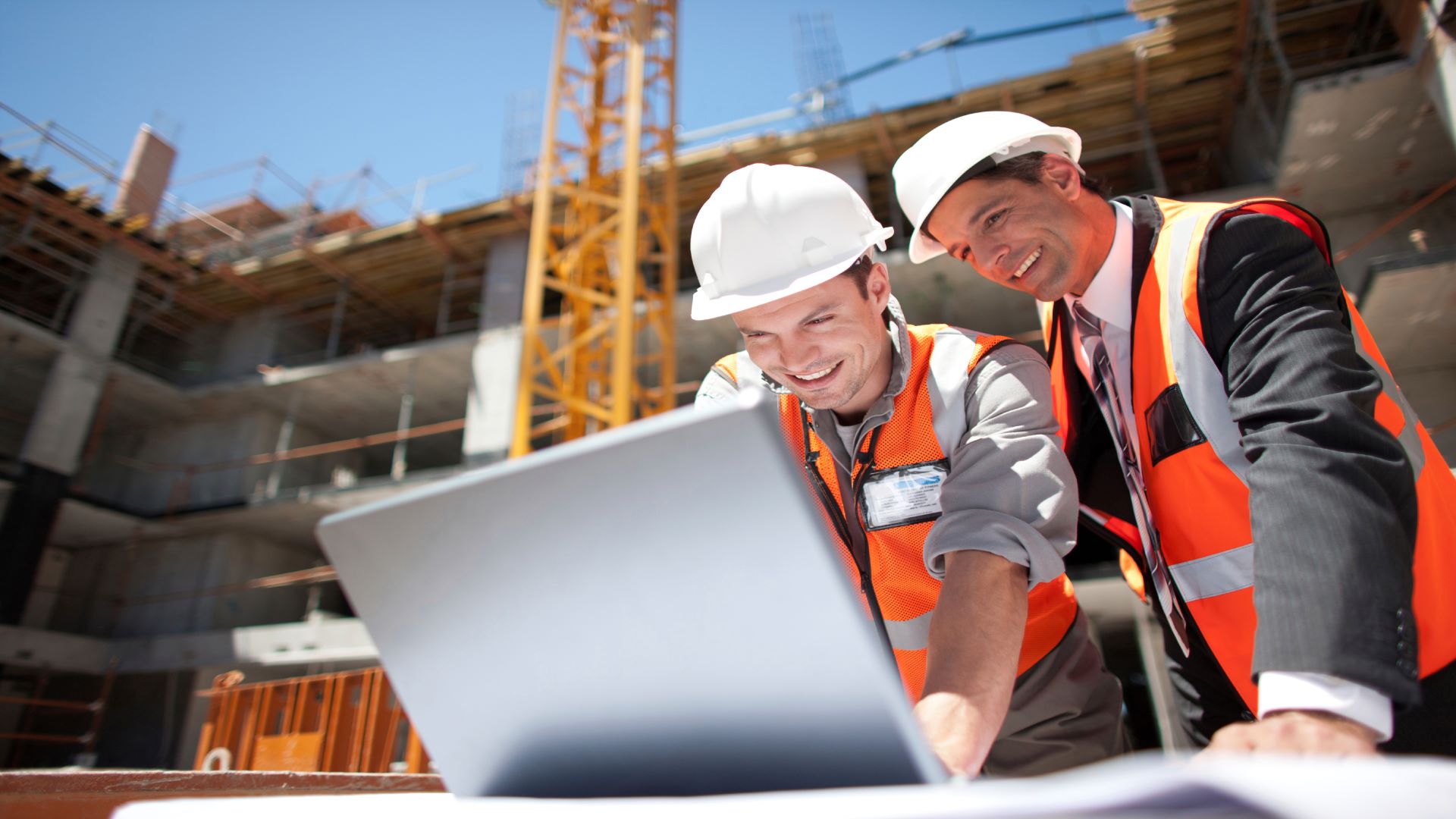
Despite accounting for 13% of the world’s GDP—making it the largest sector in the global economy—the construction industry has faced many drawbacks in recent years, resulting in a productivity growth rate of only 1% annually for the past two decades. Mounting pressure from rising costs, tighter safety and sustainability regulations, and growing consumer demands means that the already poor performance of the industry looks set to worsen. However, Rick Veague, Chief Technology Officer, North America, IFS, argues that this is the optimum time for the industry to take the digital leap. He explains the pandemic should be seen as a key opportunity for the digitalization of outdated systems and work processes.
The construction industry, that is heavily dependent on manual labor, runs on cyclical demand with low capital investment, and has a fragmented value chain which is susceptible to market downturn at the best of times, but the pandemic has hit the industry hard. Research suggests the global construction sector experienced its worst decline since the 2008 global financial crisis, falling by 3.1% in 2020. While projects have now resumed and work has started to pick up, there are still ongoing issues of supply chain shortages, human capital shortages, and rising costs that prevent full recovery.
The disruption of COVID-19 has laid bare the weaknesses in traditional construction methods and systems, so now is the perfect time to implement new digital systems as we move to create a ‘new normal’. The digital innovations that have emerged from this crisis, such as the use of IoT sensors and robotic drones, will help companies address long-term inefficiencies and adopt new processes in three key areas: improving health and safety measures, creating more sustainable practices and standardizing construction processes.
Safety First: How technology is making stringent health & safety practical
It is easy to see that health and safety have been a priority during the pandemic, and for the construction industry this is no different. In addition to conventional health and safety protocols, construction firms now use wearables and AI sensors to detect when workers are not maintaining proper physical distance. Contact tracing devices that alert employees when there are too many personnel at a worksite and can identify potentially infected individuals in the event of a confirmed COVID-19 case are also a new digital revelation. These innovations have the benefit of both ensuring employee safety and preventing site shutdowns and costly delays to project delivery.
The shift to remote work for employee safety also impacts the construction industry; new technologies such as cloud-based video platforms that assist with site monitoring have been instrumental. In the city of Miami, virtual inspections of construction sites through either a Zoom or a Microsoft Teams video call are now routine between engineers on site and building control officials. With adoption rates increasing by 239%, drones are also being used more frequently to improve mapping and surveying processes. Drones with advanced photographic capabilities can capture 360-degree views of construction sites to accurately document project progress and allow stakeholders to safely monitor and plan anywhere and anytime, improving efficiency and project delivery.
Building on sustainability with emerging technologies
Like in other industries, construction customers are demanding greater sustainability and are adding pressure for businesses to reduce carbon footprints of new constructions. Consumers are also urging companies to support the growth of a deconstruction industry that reuses huge existing stockpiles of construction material. Intense global pressure, exemplified by the UN sustainability targets, also calls for construction companies and material suppliers to incorporate sustainability into their products, construction processes, and designs.
This task will not be easy because, according to the World Green Building Council, the building and construction sectors are together responsible for 39% of all carbon emissions in the world—but technology can have a magnification effect on the effectiveness of construction green initiatives.
Structures with built in networks of Internet of Things (IoT) sensors—smart buildings—enable greater sustainability through data-driven insights. Companies can use IoT sensors and communication technology to track and monitor energy efficiency and maintenance needs. With the use of BIM (Building Information Modeling), construction companies can create a virtual 3-D model with precise transparency on all components used in a completed building, which can increase efficiency. Digital technology will enable companies to take data-driven action to improve management of building life cycles, reducing carbon footprints and waste.
Cut the risk with controlled-environment builds—modular construction 2.0
Traditional construction methods are being replaced with tech-enabled modern methods of construction (MMC) and can help overcome pressing productivity challenges. Modular construction is the process of prefabricating modules and components or even entire homes in a manufacturing facility and then shipping to the site. While not new, its recent increase in adoption rates has allowed many construction companies to continue operations in a safe, secure, and controlled way and to actively address the serious productivity problems affecting the quality and delivery pace of construction projects. McKinsey predicts that offsite construction can increase the speed of construction by as much as 50% and reduce costs, if done in the right environment, by 20%. This is achieved through the standardization of building processes—something which had not been possible before.
The wheels of digital innovation have been put in motion; it’s time for the construction industry to jump onboard
The pandemic has sparked new drive for innovation in the construction industry. The disruption of the past couples of years has highlighted the inefficiencies of traditional construction systems, and change has already started to take form, meaning there is no going back. The only way is to move forward, and technologies such as IoT sensors and data-driven systems are powerful fuel in the engine of progress. Digital transformation is the only way for the industry to, not just recover, but to thrive in the wake of the pandemic disruption.