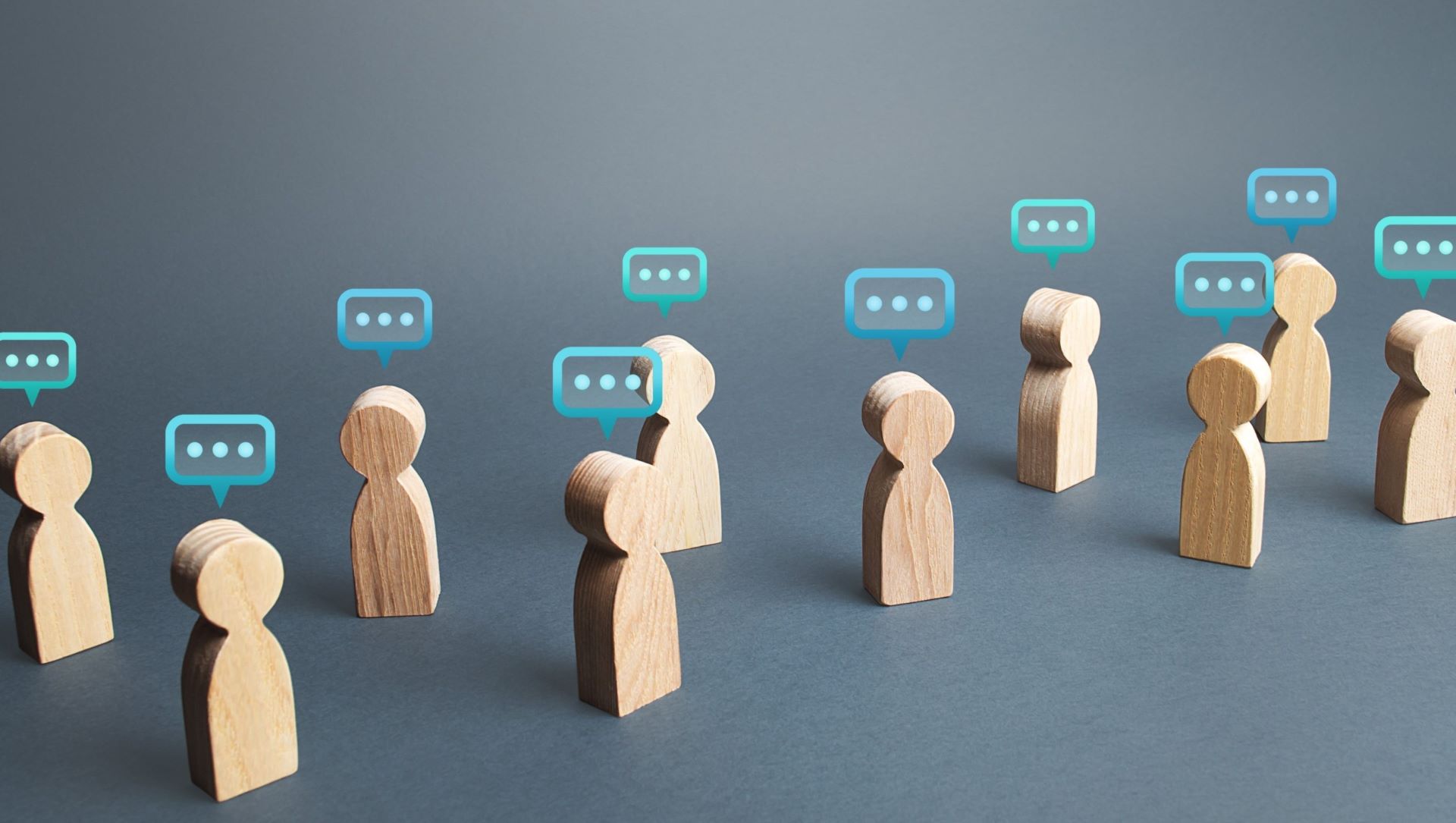
Digitalization is having a significant impact on job roles in the operational technology (OT) sector, according to a global survey of 407 industrial companies.
The Schneider Electric study, conducted in collaboration with Omdia, found 45% of these firms anticipate digitalization as the primary force behind the creation of new OT job roles within the next three years.
The study also indicated there is a widespread industrial skills crisis, with more than half (52%) of the surveyed companies grappling with talent acquisition challenges.
However, the research also noted an optimistic perspective among respondents, with more than two-thirds (70%) of survey respondents expressing the belief that digitalization will alleviate talent shortages.
Beyond just enhancing productivity, digital tools were recognized for their potential to address skill gaps effectively.
As industrial workplaces evolve rapidly, embracing sustainability goals and advanced technologies like artificial intelligence (AI) and digital twins, 45% of respondents foresee a substantial expansion of existing job roles to meet environmental and social sustainability objectives.
Despite challenges in talent acquisition and retention, 60% of participants expect OT roles to transform over the next three years, with nearly three-quarters (73%) of respondents believing that digitalization will significantly reshape the nature of work in this domain.
Stephen Kowal, chief commercial officer for Nextivity, explains as businesses evolve their wireless strategy to include public cellular coverage, private cellular, and IoT alongside Wi-Fi, enterprises – specifically those in manufacturing – will benefit from a new wave of smart automation technologies that are already addressing the current skills gap in industrial settings.
“By enabling remote visibility and control of equipment, private cellular networks allow organizations to leverage industrial IoT to optimize processes like monitoring equipment performance and tracking inventory, reducing reliance on labor that is in short supply,” he says.
From Kowal’s perspective, having a comprehensive wireless strategy boosts training quality as workers can be taught more hands-on with tools like AR and VR.
“With private cellular, warehouses can also turn to autonomous robots to handle materials and conduct inventory management,” he notes.” Already helping handle complex tasks like packaging goods nonstop, robots are making humans more productive.”
Enabled and driven by advancements in connectivity technology, robot deployment is predicted to grow at a compound rate of more than 30% per year until 2030.
“Looking ahead to 2024, organizations will increasingly focus on improving connectivity technology within their businesses to raise the productivity of their workforce and alleviate talent skills issues,” Kowal adds.
The Schneider Electric survey also revealed a growing demand for new skills, particularly in robotics programming and integration, where just under half (49%) of respondents lacked adequate skills, and in data processing, visualization and analytics, where more than 30% had insufficient expertise.
While companies prioritize investments in data-related skills, robotics programming and integration ranked as a medium priority for nearly half of those surveyed.
The report noted the importance of industrial companies collaborating with ecosystem partners to bridge technology skill gaps through training, solutions, and capabilities to prepare their workforce for the imminent future.
Juniper CIO Sharon Mandell points out that in today’s tech landscape, CIOs and leaders are turning to automation and AI to meet growing business demands.
“These tools not only offer a strategic solution to talent shortages but can also empower existing teams,” she says. “If AI-powered solutions and automation can assist in keeping vital technology infrastructure working, organizations can invest greater resources in job creation and revenue-generating initiatives.”
Mandell adds the adoption of automation should go hand-in-hand with a commitment to ongoing training and education.
“When employees are equipped with the right automation tools and skills, they can spend more energy on high-value work, leading to greater creativity, innovation and job satisfaction,” she says.