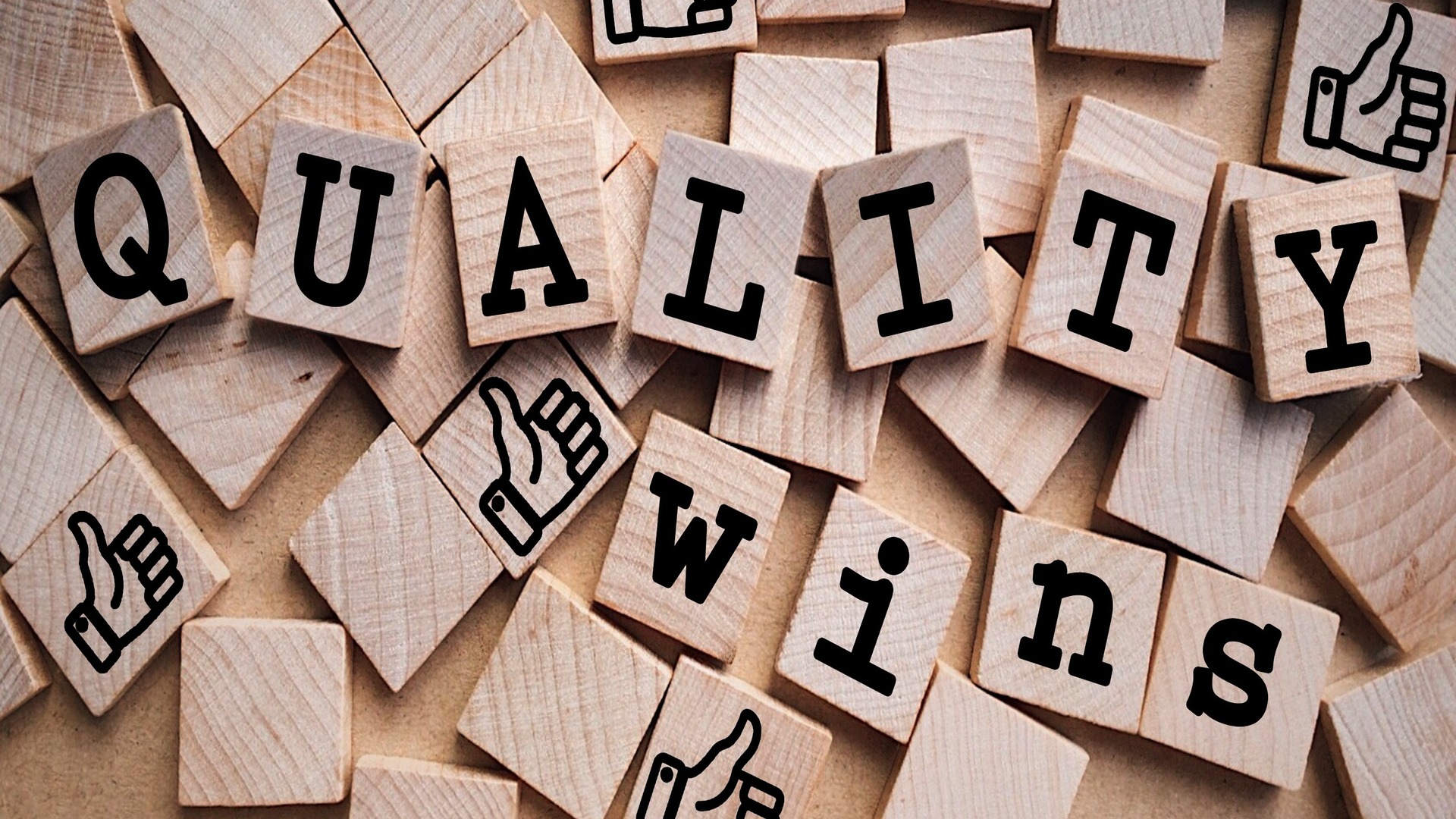
In the competitive world of manufacturing, maintaining high standards of quality is not just a necessity, it is a critical differentiator. Quality management systems like Six Sigma, Lean and Total Quality Management have emerged as indispensable tools, driving continuous improvement, reducing waste and enhancing customer satisfaction. Implementing these systems requires a strategic approach and an understanding of the unique needs of the manufacturing environment.
Six Sigma is a data-driven methodology that aims to improve processes by identifying and removing causes of defects and minimizing variability in manufacturing and business processes. It uses statistical methods to achieve near-perfection, intending to reach a defect rate of no more than 3.4 defects per million opportunities. Six Sigma follows the DMAIC (Define, Measure, Analyze, Improve, and Control) framework, guiding organizations through a systematic approach to problem-solving.
Lean Manufacturing, another popular QMS, focuses on waste reduction and efficiency. By eliminating non-value-added activities, Lean aims to streamline production processes, reduce costs and improve product quality. It often works hand-in-hand with Six Sigma to address both waste and defects.
Total Quality Management is a broader approach that encompasses the entire organization, promoting a culture of continuous improvement, customer focus and employee involvement. TQM is more about the overall philosophy of quality management rather than specific tools and techniques, making it a holistic approach to achieving excellence in manufacturing.
Interested? Here are the Key Steps for Implementing Six Sigma in Manufacturing:
- Top Management Commitment and Support: The successful implementation of Six Sigma starts at the top. Management must be fully committed to the process, providing resources, setting clear goals, and fostering a culture of improvement. Without strong leadership, Six Sigma initiatives are likely to falter. General Electric is a classic example of Six Sigma implementation driven by top management. When Jack Welch, the then-CEO, made Six Sigma a strategic priority in the 1990s, the company saw a significant reduction in defects, leading to billions of dollars in cost savings.
- Training and Development: Six Sigma relies heavily on skilled practitioners, known as Green Belts, Black Belts, and Master Black Belts, who lead improvement projects. Comprehensive training programs are essential to equip employees with the tools and techniques of Six Sigma, such as statistical analysis, process mapping, and root cause analysis. Motorola, the originator of Six Sigma, invested heavily in training its employees. By educating its workforce on Six Sigma methodologies, Motorola was able to reduce its defect rate significantly and set a new standard for quality in the electronics industry.
- Project Selection and Prioritization: Not all problems in a manufacturing process require a Six Sigma project. It’s crucial to select projects that align with the organization’s strategic goals and have a significant impact on quality and customer satisfaction. The selected projects should be prioritized based on their potential for improvement and the resources available. For instance, in the automotive industry, Ford Motor Company implemented Six Sigma to address quality issues in their production lines. By focusing on high-impact areas such as paint quality and engine assembly, Ford was able to reduce defects and improve customer satisfaction, leading to higher sales and brand loyalty.
- Data-Driven Decision Making: One of the core principles of Six Sigma is making decisions based on data rather than assumptions. This requires collecting and analyzing data to identify root causes of defects and measure the effectiveness of improvements. Tools like control charts, Pareto analysis and failure mode and effects analysis (FMEA) are commonly used in this phase. Texas Instruments applied Six Sigma to their semiconductor manufacturing process by analyzing data to identify variations in production. Through rigorous data analysis, they were able to reduce variability, leading to higher yields and lower production costs.
- Sustaining Improvements: After implementing improvements, the gains achieved must be sustained over time. This involves establishing control plans, standardizing processes and regularly monitoring KPIs to detect any signs of regression. At Honeywell, Six Sigma projects are closely monitored even after implementation. The company uses a structured control phase to maintain the improvements made, ensuring long-term benefits such as cost savings and enhanced product reliability.
While Six Sigma is a powerful tool, integrating it with other QMS can amplify its benefits. Lean Manufacturing and TQM can complement Six Sigma by addressing different aspects of quality and efficiency in manufacturing.
- Lean Six Sigma: By combining the waste reduction focus of Lean with the defect reduction focus of Six Sigma, Lean Six Sigma provides a comprehensive approach to process improvement. Lean Six Sigma projects typically begin with identifying waste in the process, followed by applying Six Sigma techniques to eliminate defects. Toyota, known for its Toyota Production System, also integrates Six Sigma principles in its production system. By doing so, Toyota not only minimizes waste but also ensures that its processes are highly reliable and produce defect-free products.
- Total Quality Management: TQM’s focus on organizational culture and employee involvement can enhance the effectiveness of Six Sigma. While Six Sigma provides the tools for improvement, TQM ensures that the entire organization is aligned toward quality goals. This holistic approach can lead to more sustainable improvements. IBM integrated TQM with Six Sigma to improve its customer service operations. By fostering a culture of quality across all levels of the organization, IBM was able to achieve significant improvements in customer satisfaction and operational efficiency.
Despite the benefits, implementing Six Sigma and other QMS in manufacturing is not without challenges. Common obstacles include a possible resistance to change by employees, lack of resources and insufficient training. To overcome these challenges, it is essential to communicate the benefits of these systems, involve employees in the process and provide ongoing support and training.
Implementing Six Sigma and other quality management systems in manufacturing can lead to significant improvements in product quality, operational efficiency and customer satisfaction. By following a structured approach, investing in training and integrating multiple QMS methodologies, manufacturers can achieve continuous improvement and maintain a competitive edge in the market. The examples of companies like GE, Motorola, Ford and Toyota demonstrate the transformative power of these systems when implemented effectively. However, success depends on strong leadership, a data-driven approach and a commitment to fostering a culture of quality throughout the organization.